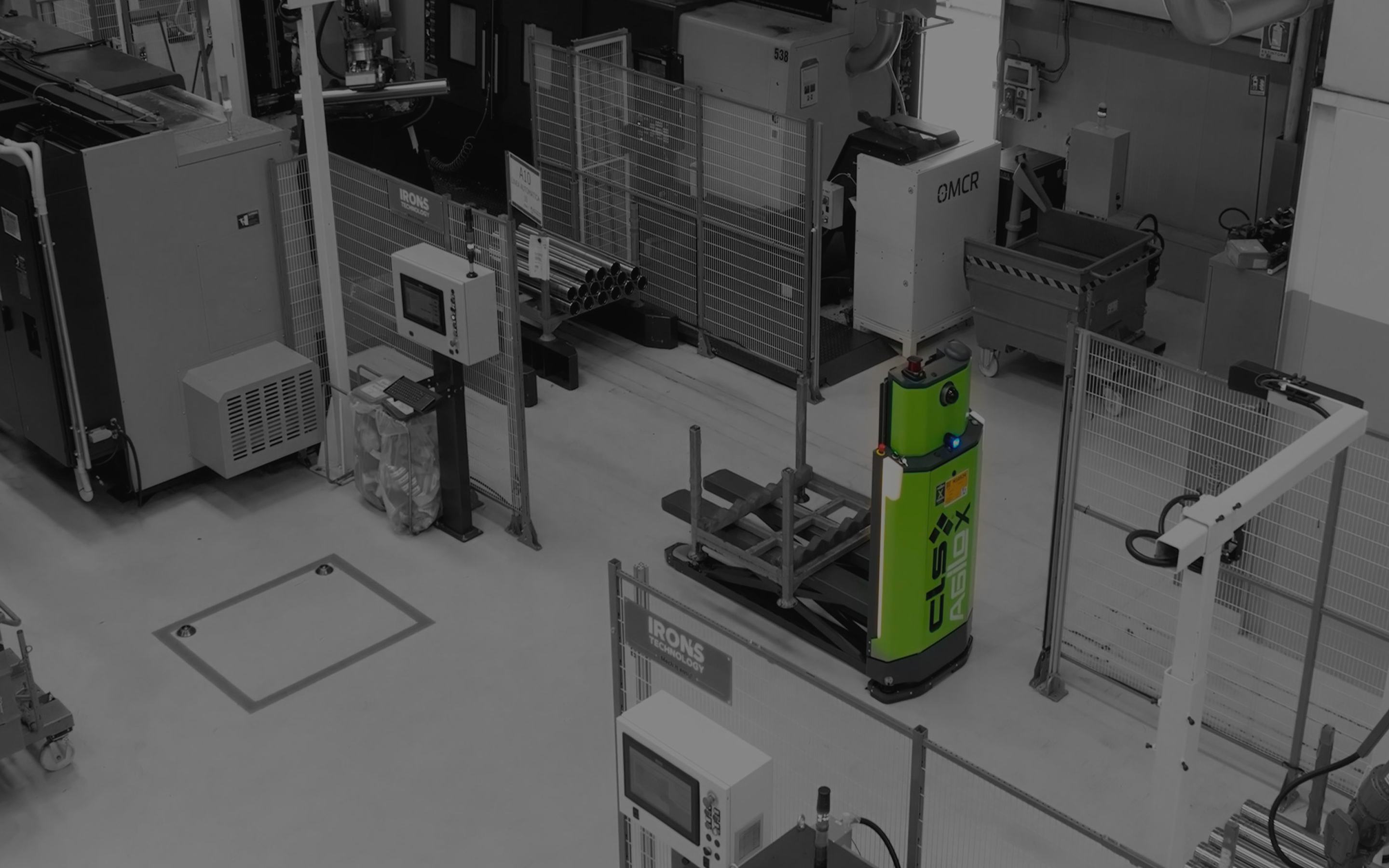
INTERPUMP HYDRAULICS
HOW INTERPUMP HYDRAULICS HAS
OPTIMISED PRODUCTION WITH DYMATION.
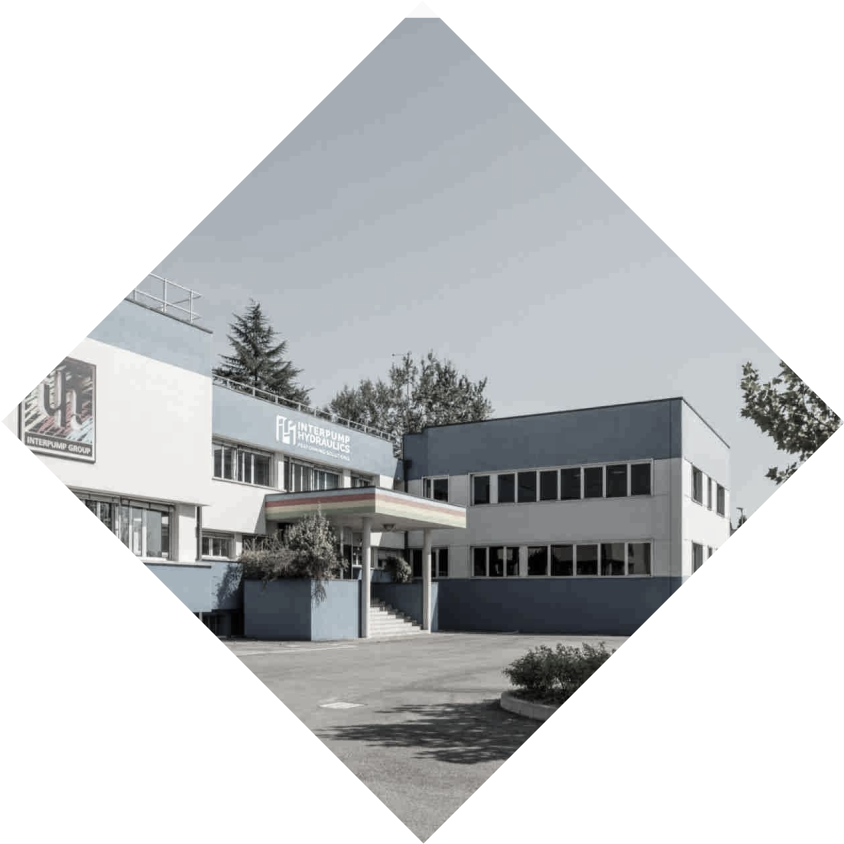
CUSTOMER INTRODUCTION
Interpump is a leading company in the production of telescopic cylinders.
Interpump is a leading company in the production of telescopic cylinders, with a manufacturing plant located in Faenza. Its product range includes front cylinders, double-acting telescopic cylinders, lightweight cylinders, and under-body cylinders. The launch of the new front cylinder Series 5 required an increase in production capacity, prompting the company to invest in a new automated turning island. Thanks to the collaboration with Dymation, Yaskawa, and Iron’s Technology, an innovative system was developed for the production of this new solution.
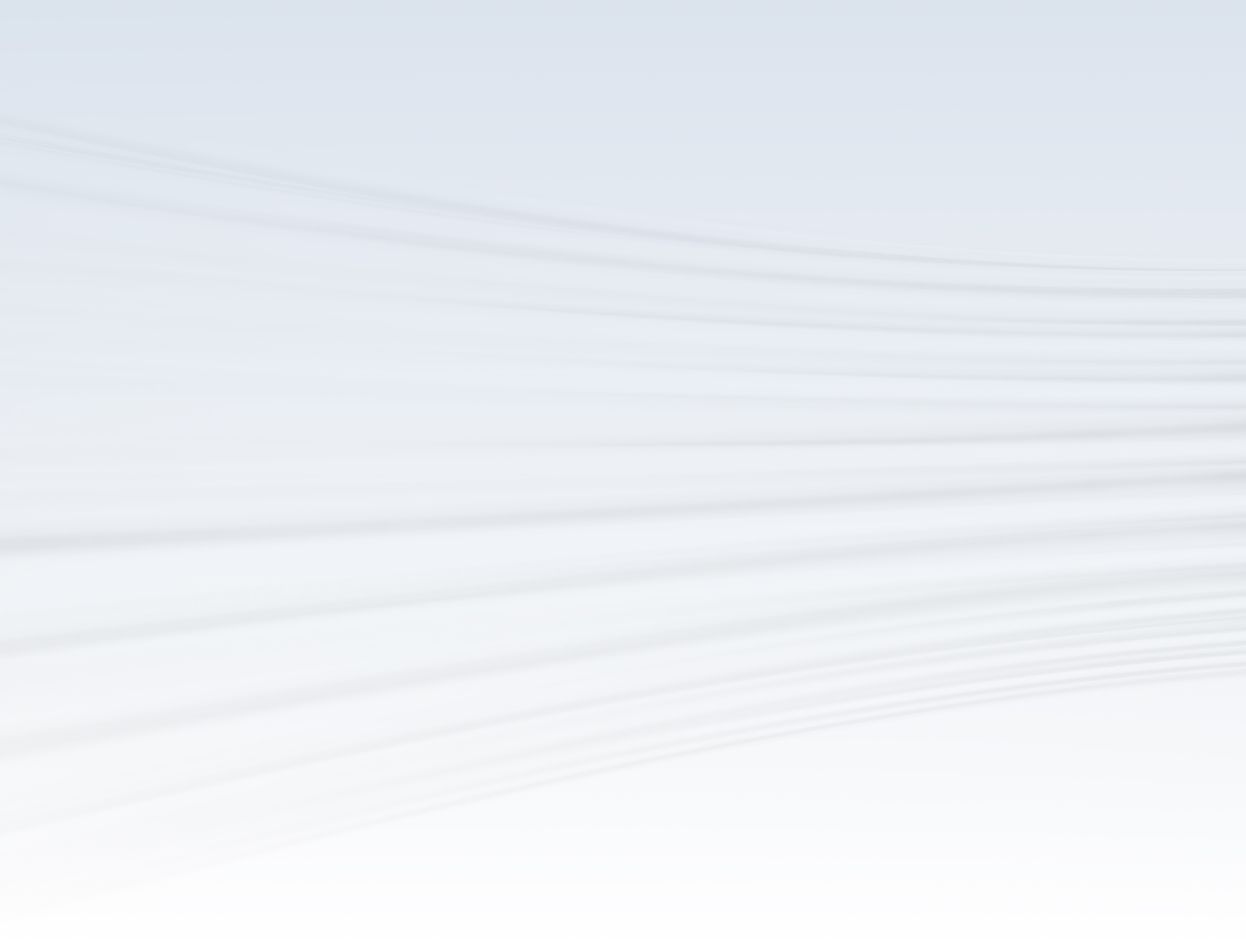
The company faced a significant challenge: increasing production capacity to meet the growing demand for the new Series 5 front cylinder without compromising efficiency and quality. The goal was to implement an automated system capable of improving workflow, ensuring continuous production monitoring, and optimizing human resources while maintaining high safety and reliability standards. However, to achieve these results, Interpump had to overcome several problems that hindered the process:
- Need to increase production capacity
- Automation of the workflow
- Monitoring and remote control
- Safety and reliability
- Optimization of human resources
Dymation implemented an advanced automation system based on an Autonomous Mobile Robot (AMR) interconnected with four industrial robots through a dedicated management software. This system:
- Increased production capacity: Thanks to automation, the company increased production volume without expanding its workforce.
- Improved quality control: The automated system ensures superior precision in assembly and quality checks, reducing waste and rework.
- Reduced operational costs: Process optimization lowered production costs, enhancing the company’s profitability.
- Better workforce utilization: Operators, freed from manual tasks, were reassigned to more strategically valuable roles.
- Safety and reliability: The customized AMR improved the handling of heavy loads, reducing accident risks and enhancing working conditions.
Thanks to these achievements, the company has decided to extend the system to other workstations, reinforcing its commitment to continuous innovation and process improvement.
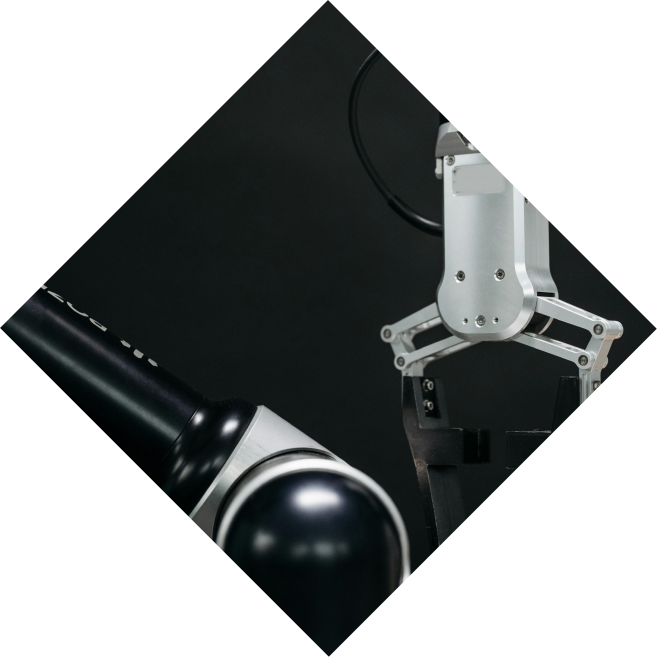
Dymation turns potential into competitiveness.
Change becomes efficiency.
Tomorrow becomes today.
This is innovation, with Dymation.