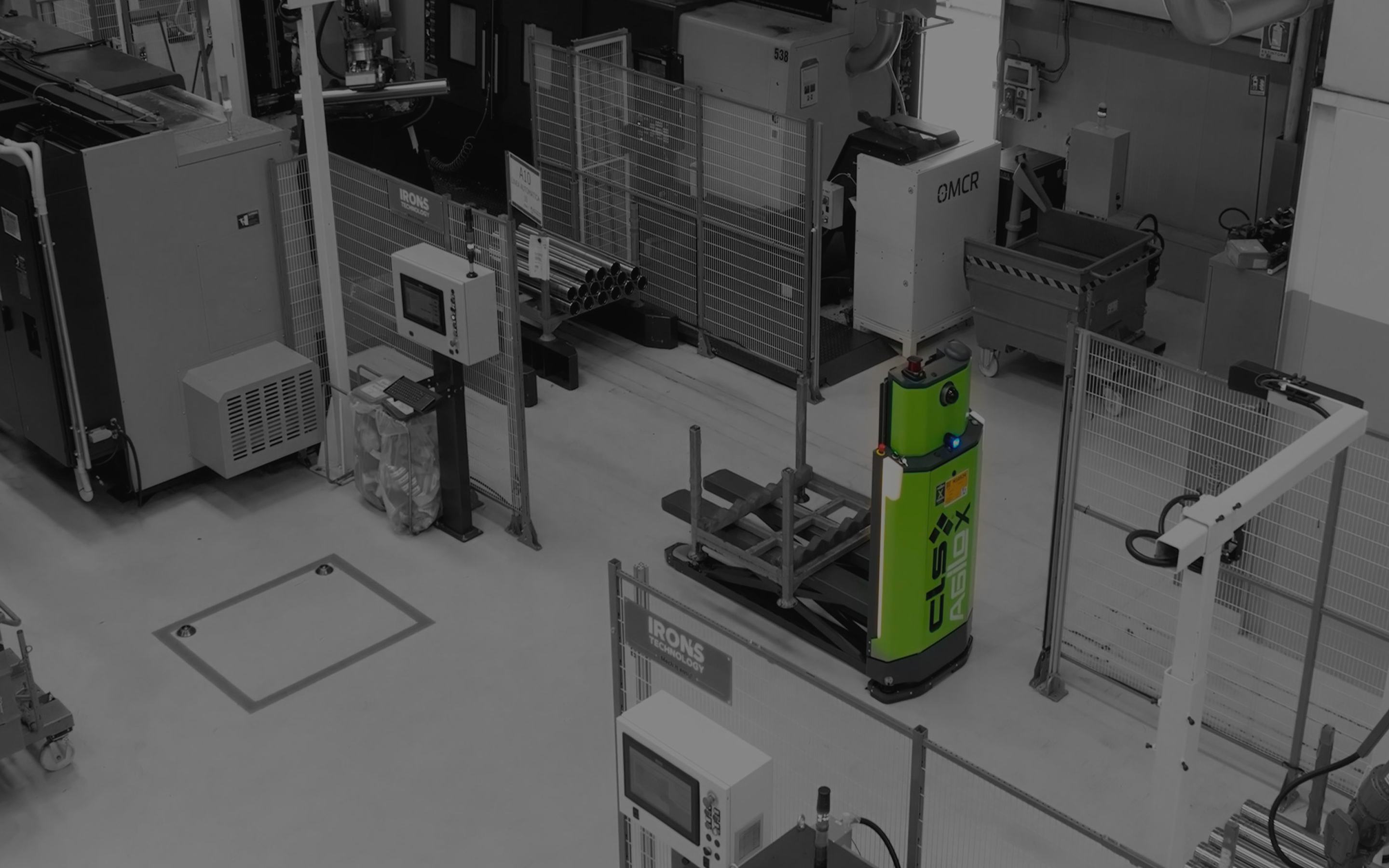
INTERPUMP HYDRAULICS
COME INTERPUMP HYDRAULICS HA
OTTIMIZZATO LA PRODUZIONE CON DYMATION.
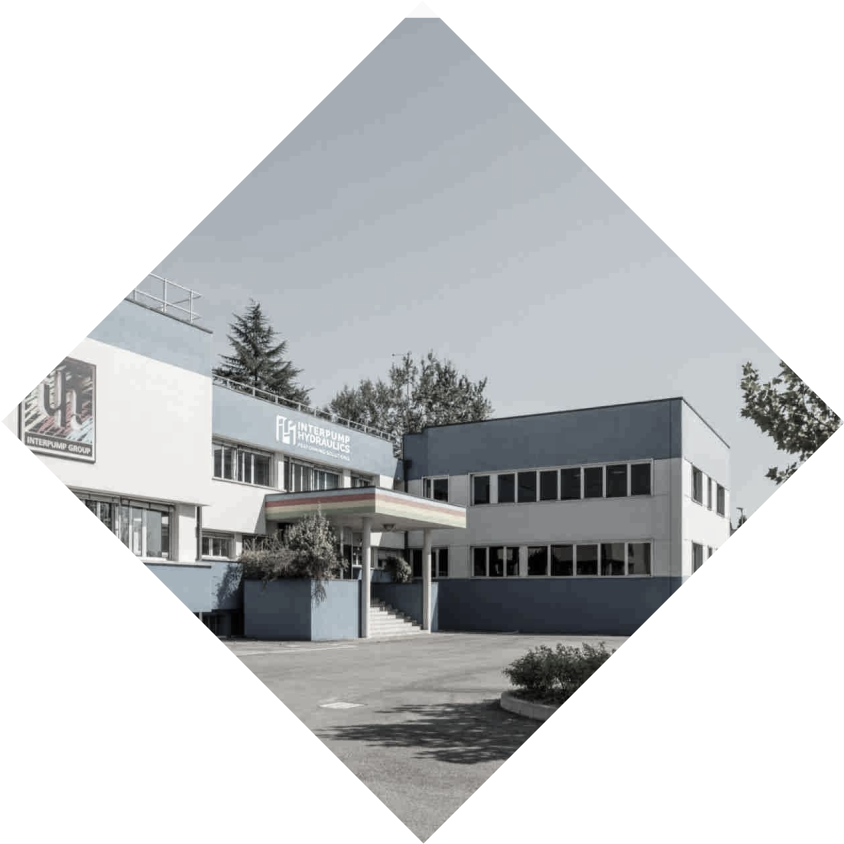
INTRODUZIONE AL CLIENTE
Interpump è un’azienda leader nella produzione di cilindri telescopici.
Interpump è un’azienda leader nella produzione di cilindri telescopici, con uno stabilimento situato a Faenza. La gamma di prodotti comprende cilindri frontali, cilindri telescopici a doppio effetto, cilindri leggeri e cilindri sottocassa. L’uscita sul mercato del nuovo cilindro frontale Serie 5 ha reso necessario un aumento della capacità produttiva, portando l’azienda a investire in una nuova isola di tornitura automatizzata. Grazie alla collaborazione con Dymation, Yaskawa e Iron’s Technology, è stato realizzato un impianto innovativo per la produzione di questa nuova soluzione.
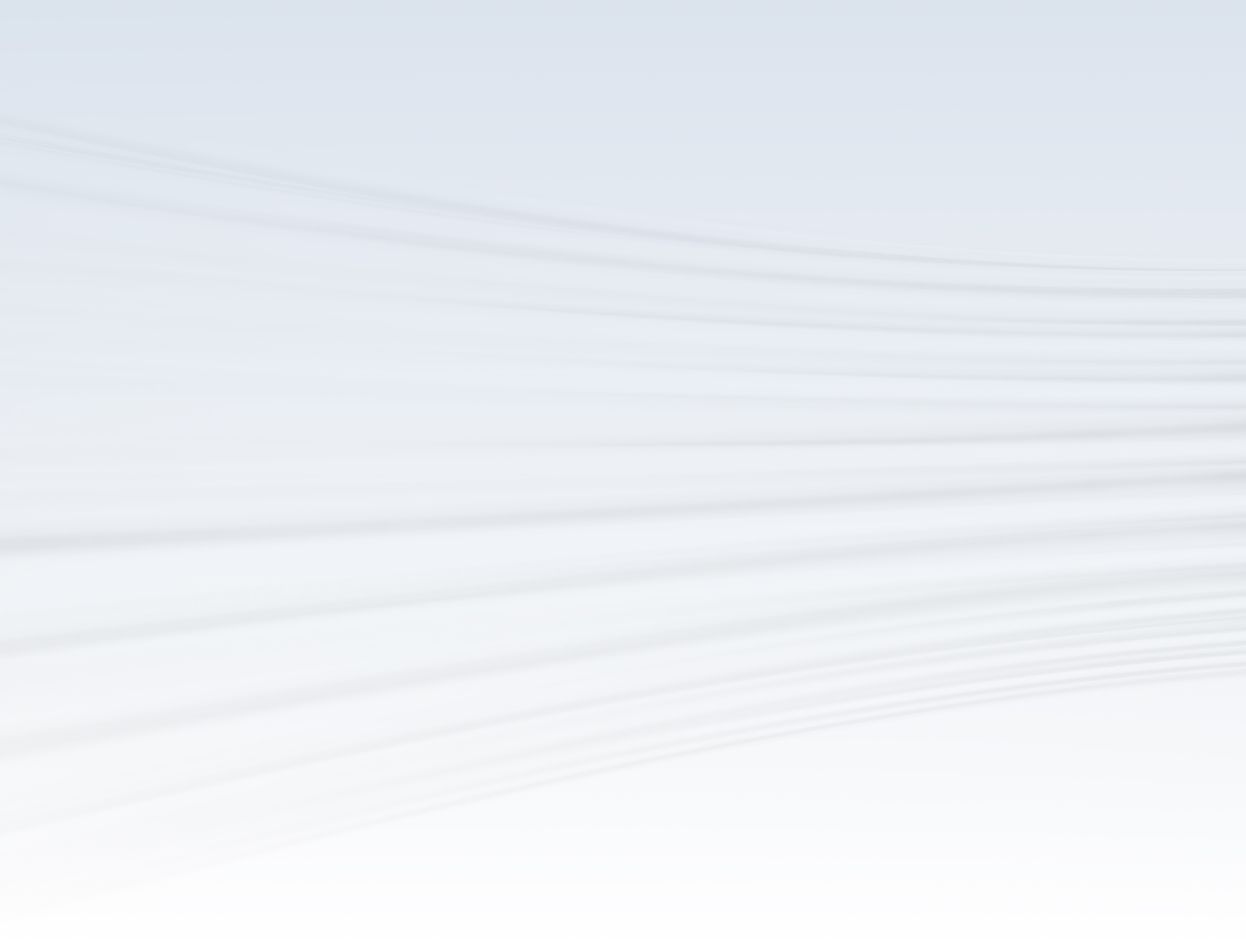
L’azienda si è trovata di fronte a un’importante sfida: aumentare la capacità produttiva per far fronte alla crescente domanda del nuovo cilindro frontale Serie 5, senza compromettere l’efficienza e la qualità. L’obiettivo era implementare un sistema automatizzato capace di migliorare il flusso di lavoro, garantire un monitoraggio continuo della produzione e ottimizzare le risorse umane, mantenendo alti standard di sicurezza e affidabilità. Tuttavia, per raggiungere questi risultati, Interpump ha dovuto affrontare una serie di problemi che ostacolavano il processo.
- Necessità di aumentare la capacità produttiva
- Automazione del flusso di lavoro
- Monitoraggio e controllo remoto
- Sicurezza e affidabilità
- Ottimizzazione delle risorse umane
Dymation ha implementato un sistema di automazione avanzato basato su un AMR (Autonomous Mobile Robot) interconnesso con quattro robot industriali tramite un gestionale dedicato. Questo sistema:
- Aumento della capacità produttiva: Grazie all’automazione, l’azienda ha incrementato il volume di produzione senza aumentare il numero di operatori.
- Maggiore controllo della qualità: Il sistema automatizzato garantisce una precisione superiore nell’assemblaggio e nel controllo qualità, riducendo scarti e rilavorazioni.
- Riduzione dei costi operativi: L’ottimizzazione del processo ha abbassato i costi di produzione, migliorando la redditività aziendale.
- Migliore impiego del personale: Gli operatori, liberati da compiti manuali, sono stati riassegnati a mansioni di maggior valore strategico.
- Sicurezza e affidabilità: L’ottimizzazione del processo ha abbassato i costi di produzione, migliorando la redditività aziendale.
Grazie ai risultati ottenuti, l’azienda ha deciso di estendere il sistema anche ad altri centri di lavoro, confermando la propria volontà di innovare e migliorare continuamente i propri processi produttivi.
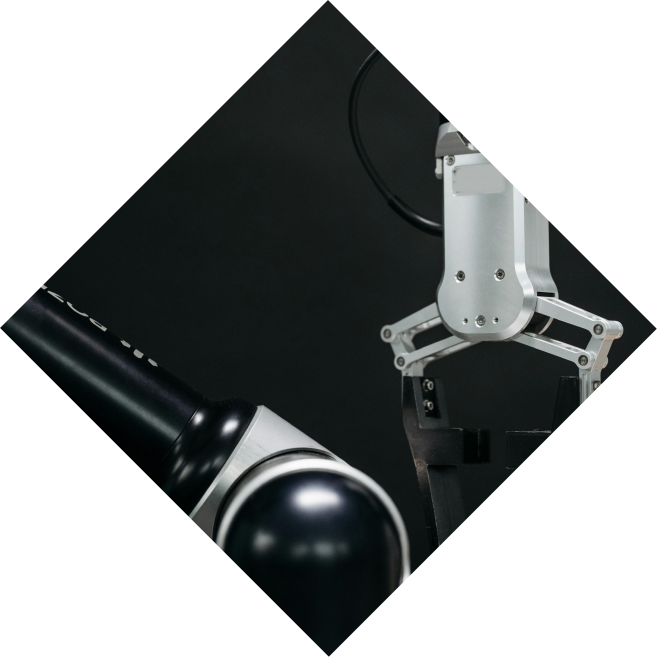
Convertiamo il potenziale in competitività.
Il cambiamento in efficienza. Il domani nell’oggi.
E lo chiamiamo innovazione.